Engineers utilise partial discharge testing as a diagnostic method to evaluate the health and integrity of high-voltage insulating systems. It is necessary to locate and measure partial discharges, or localised electrical discharges, within insulating materials under high-voltage stress. These discharges might eventually damage the insulation, leading to insulation failure and ultimately device failure.
Identification, localization, and evaluation of the severity of partial discharges in electrical systems or equipment are the primary goals of partial discharge testing. Engineers can assess the insulation's quality, spot any flaws or problems, and decide whether to maintain, repair, or replace the equipment by spotting and monitoring partial discharges.
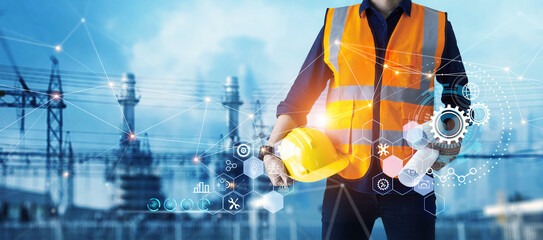
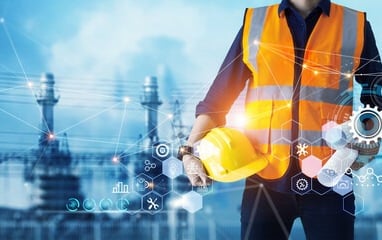
What is Partial Discharge Testing?
Partial discharge testing assesses the insulation condition in high-voltage electrical equipment. It involves detecting and measuring the partial discharges within the insulation system.
Partial discharges are small electrical sparks or arcs that can happen within voids, air pockets, or defects in the insulation material. These discharges generate high-frequency electrical signals, acoustic emissions, or electromagnetic waves that can be detected and analyzed.
The purpose of partial discharge testing is to identify potential faults or weaknesses in the insulation system that could lead to insulation breakdown, equipment failure, or safety hazards. By detecting and monitoring partial discharge activity, maintenance teams can assess the condition of the insulation, identify early signs of deterioration, and take appropriate actions to prevent further damage.
Partial Discharge Testing
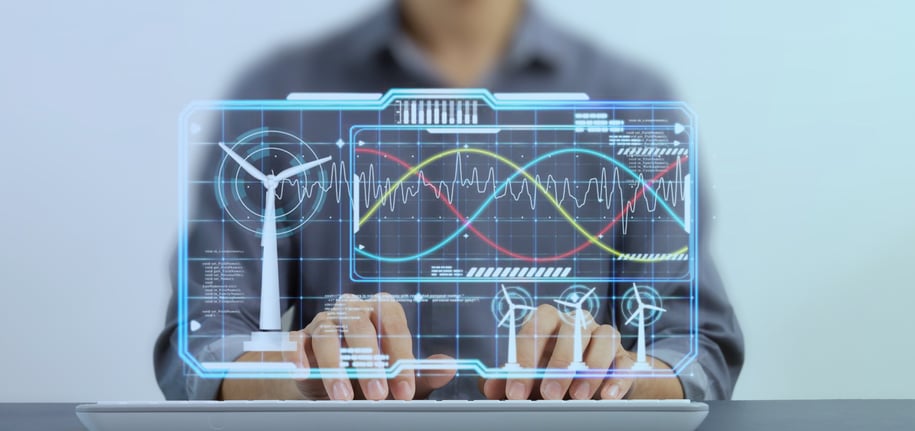
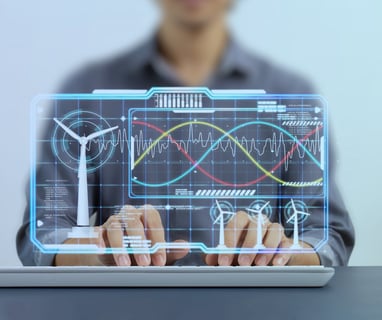
How many types of partial discharge testing are there?
There are several types of partial discharge testing techniques available. Here are some commonly used ones:
1. Electrical Partial Discharge Measurement: This technique measures the electrical signals generated by partial discharges. It can be done using various instruments, such as partial discharge analyzers, which capture and analyze the discharge signals.
2. High-Frequency Current Transformer (HFCT) Method: HFCT is a technique where a high-frequency current transformer is placed around the cable or equipment being tested. It detects the high-frequency signals generated by partial discharges.
3. Ultrasonic Detection: This method uses ultrasonic sensors to detect the acoustic signals produced by partial discharges. It effectively detects partial discharges in gas-insulated switchgear (GIS) or other enclosed systems.
4. Transient Earth Voltage (TEV) Detection: TEV testing involves measuring the transient voltages induced on the surface of the equipment due to partial discharges. It utilizes sensors placed on the outer surface of the equipment.
5. Radio Frequency (RF) Detection: RF detection involves capturing the radio frequency electromagnetic waves emitted by partial discharges. This technique is often used for testing high-voltage cables and power transformers.
6. Capacitive Coupling (CC) Detection: CC testing uses capacitive couplers to detect partial discharge signals. It involves coupling the signals from the equipment under test to the measuring instrument through capacitive plates or sensors.
Importance of Partial Discharge Testing
The study of partial discharges is essential for electrical engineering and power systems. The following are some significant arguments in favour of partial discharge testing:
1. Evaluation of Insulation Condition: Partial discharge testing offers essential information on the health and integrity of insulation systems in high-voltage machinery. It assists in locating any flaws, imperfections, or ageing effects that could cause insulation failure.
2. Risk reduction : Assessing and measuring the risk associated with the systems is aided by testing for partial discharges. Engineers can determine the likelihood of insulation failure and the risk of equipment failure by looking at the severity and features of partial discharges.
3. Diagnostic Tool for Fault Location: Partial discharge testing can be used to find insulation flaws in electrical equipment. By analysing the types and distribution of partial discharges, engineers can pinpoint the areas where insulation degradation takes place.
Why is a Partial Discharge Test Needed?
Partial discharge testing is needed for several reasons that can maintain the insulation deterioration in electrical equipment
1. Early Fault Detection: Partial discharge activity indicates insulation deterioration in high-voltage electrical equipment. Conducting partial discharge tests can detect potential faults or weaknesses in the insulation system early. It allows for proactive maintenance and repair, preventing more severe failures or breakdowns in the future.
2. Insulation Condition Assessment: Partial discharge testing helps assess the insulation condition in high-voltage equipment. Insulation breakdown can lead to equipment failure, safety hazards, and costly downtime. By evaluating the magnitude and pattern of partial discharge activity, engineers can determine the overall health and integrity of the insulation system.
3. Quality Assurance during Manufacturing: Partial discharge testing is essential during the manufacturing process of high-voltage equipment. It helps ensure that the insulation meets the required standards and specifications. By performing tests on newly manufactured equipment, manufacturers can identify any insulation defects or issues before the products are deployed in the field.
4. Preventive Maintenance and Asset Management: Partial discharge testing is vital for preventive maintenance and asset management programs. By regularly monitoring partial discharge activity in electrical assets, maintenance teams can schedule maintenance or replacement activities based on the condition of the insulation. This approach helps avoid unexpected failures, reduces downtime, and extends the lifespan of the equipment.
5. Safety and Reliability: For high-voltage electrical systems to be safe and dependable, partial discharge testing is essential. By identifying potential insulation defects or weaknesses, necessary repairs or replacements can be carried out, reducing the risk of catastrophic failures, electrical accidents, and power outages.
Why Choose Eternegy?
Here are a few arguments in favour of choosing Eternegy:
1. Creative Solutions: Eternegy includes creative solutions for developing systems, operations, and processes in their finished works and projects. Their dedication to innovation shows that they make an effort to keep up with industry developments and provide cutting-edge services to their clients.
2. Eternegy conducts thorough examinations of engineering practices, operations, onsite functionality, and partial discharge testing for electrical systems and equipment.
3. Cohesive Approach: In order to continue its development, Eternegy uses a cohesive approach. They demonstrate a commitment to evolving and enhancing their practices over time by making minor, progressive improvements to their offerings, leading to greater outcomes for their customers.
4. Adaptable Methodologies: The testing, design, and commissioning phases of Eternegy's projects are all handled using agile techniques. Agile practices allow for quick adjustments with project requirements.